Yamazumi
Cześć, jestem Adam i od ponad 20 lat zajmuję się optymalizacją Procesów. Chciałbym za pomocą prawdziwej historii pokazać Wam, jak możecie wykorzystać narzędzie do balansowania linii, jakim jest Yamazumi Chart (zwany również inaczej Line Balance Chart).
Firma w której miałem przyjemność pracować miała fabryki na każdy kontynencie (poza Antarktydą i Australią). Dostałem kiedyś propozycję: w dalekim kraju (nazwy nie podaję, żeby nie wzbudzać emocji) jest fabryka a tam wkrótce na pewnej linii produkcyjnej nie będą w stanie zaspokoić oczekiwań klienta. Należy zwiększyć liczbę szt./godz z 40 do 60. Oni mają już pomysł, jak to zrobić, ale może mógłbyś pomóc?
Skoro już wiedzą, jak to zrobić, to chyba nie jestem potrzeby? Na ale z drugiej strony w tym kraju jeszcze nie byłem. Czego nie robi się dla firmy ;-).
Załóżmy, że za produkcję odpowiedzialny jest Johannes, za Continuous Improvement Thomas a szefem zakładu jest Raymond. Dostałem coś co było w mniemaniu Johannes studium przypadku. Mogę w skrócie to opisać następująco: „Na linii montażowej mamy 8 stanowisk, produkujemy maks. 40 szt./godz. Chcemy dołożyć stanowisko pomiędzy stacją 2 i 3”. Imponujące(!), a jak do tego doszliście?
Kilka pytań sprawdzających w przypadku linii produkcyjnej:
· – Czy znamy czasy operacji na każdej stacji?
· – Czy mamy podział operacji na VA i NVA?
· – Jaka jest relacja czasów do T/T?
Generalnie wystarczy pokazać jeden wykres – Line Balance Chart, aby móc odpowiedzieć na większość pytań. Tak się dobrze składa, gdyż przygotowałem dla Was Line Balance Chart do pobrania. Czasami zdarza się, że ktoś pokazuje taki wykres jak na Rys. 1 i mówi, że to LB chart. Można się kłócić o nazwy, ale ja nazywam to Analizą Wąskiego Gardła (Bottleneck Analisys), gdyż w zasadzie widzimy, tylko:
– Sumaryczny czas operacji na stacjach.
– Różnicę między czasami, w tym najdłuższy czas.
– Czy mieścimy się w T/T?
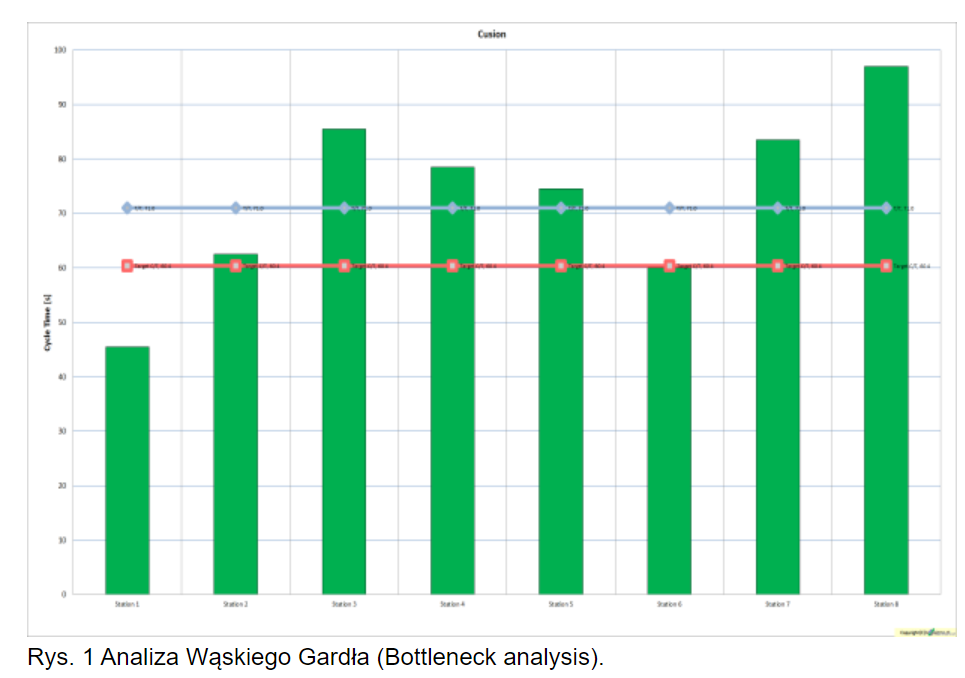
Muszę jeszcze wyjaśnić, dlaczego widzimy 2 linie poziome na Rys. 1. Pierwsza linia na poziomie 71 s, to T/T (Takt Time), druga to Target C/T (Target Cycle Time), która jest wyliczana na podstawie T/T i OEE (MU). C/T (Cycle Time) na każdej stacji (wysokość słupka na wykresie) powinien być mniejszy lub równy Target C/T.
Zaproponowałem, że zrobię filmy na każdym stanowisku oraz zrobię analizę Line Balance (Yamazumi)? Spędziłem kilkanaście godzin na linii produkcyjnej. Zrobiłem kilkanaście filmów, które obejmowały wszystkie Stacje i jeżeli to było możliwe różnych operatorów na tych samych Stacjach. Nagrałem również operacje automatyczne, w tym wypadku stanowisko do testowania produktów (Stacja 7).
2 dni później zaprosiłem Raymonda, Johannesa i Thomasa na prezentację mojej analizy (Rys. 2). Zanim pokazałem LB Chart zacząłem od filmu ze Stacji 1. Trwał ok 45 sek. Zadałem pytanie: jaki % czasu wypełniają czynności dodające wartości (Value Adding – VA)? Raymond odpowiedział pewnym głosem ok. 80%. Wiedziałem już, że mamy kolejny problem (pierwszy to ustalenia na czuja, że chcemy dodać nowe stanowisko pomiędzy Stacją 2 a Stacją 3). Jak to powiedzieć, żeby nikogo nie urazić? Powiedziałem: „Zobaczmy zatem do pliku LB i sprawdźmy poszczególne czynności”. Zrobiliśmy wspólną analizę operacji i sprawdziliśmy, czy mój podziałem na czynności dodające wartości (VA) i niedodające wartości (NVA) jest prawidłowy. A teraz podsumujmy – powiedziałem: „VA czynności stanowią ok. 20%(!)”. Zapadła niezręczna cisza…
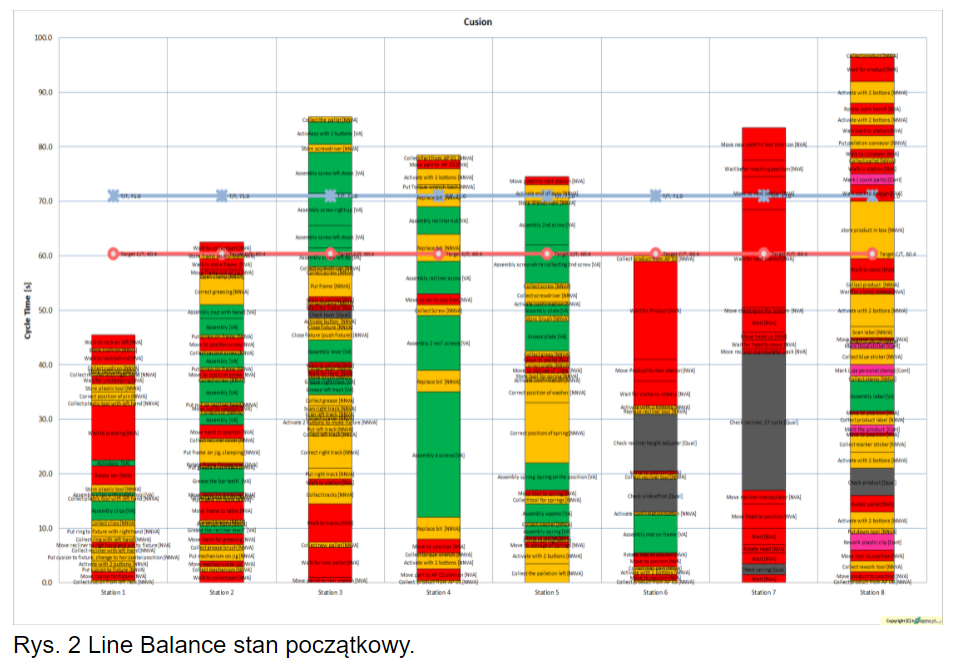
Proszę zwrócić uwagę, że operacje dodające wartości (VA) są zaznaczone na Rys. 2 na zielono i stanowią między 20% a 80% w zależności od Stacji.
Co jest nie tak z Raymondem, czy on nie ma pojęcia o produkcji? Nie wyciągajmy pochopnych wniosków. Kiedy oglądasz film, łatwo wychwycić Czekanie (jedno z 8 marnotrawstw) – tu nie mamy wątpliwości. Czekanie na pewno nie jest VA. Kiedy widzisz, że operator coś robi, to często uznajesz, że to czynność VA i tu niestety intuicja może nas zawieść.
Wróćmy do definicji czynności VA. Pamiętacie? VA to czynność, która zmienia formę lub funkcję produktu, została zrobiona prawidłowo za pierwszym razem oraz klient jest skłonny za to zapłacić (czyli jest w specyfikacji produktu). Wszystko inne po prostu nie jest VA.
Gdy już wyjaśniłem zawiłości z operacjami VA i NVA, pokazałem wykres prezentowany na Rys. 2, dla każdej Stacji podałem listę usprawnień, która wynikała z analizy czasów poszczególnych czynności. Coś można było zrobić szybciej przez inne ułożenie materiałów, z czegoś można był zrezygnować itd. Dla każdego stanowiska oszacowałem nowy C/T, który zaprezentowałem na Rys. 3.
Dużym zaskoczeniem była analiza Automatycznej Stacji Testowej (Stacja 7). Pokazałem jaką drogę pokonuje głowica testowa, ile czasu produkt czeka przed testowaniem itd. Raymonda, Johannesa i Thomasa nie mieli pojęcia, że to również wąskie gardło oraz że możliwości poprawy czasów są bardzo obiecujące. Cały potencjał widać przy porównaniu Rys. 2 i Rys. 3. Znaczną poprawę można osiągnąć na Stacji 1, Stacji 3 i Stacji 7. Moje analizy zostały zaakceptowane, mimo że był całkowicie niezgodne z wcześniejszymi analizami pochodzącymi z fabryki oraz intuicją moich kolegów.
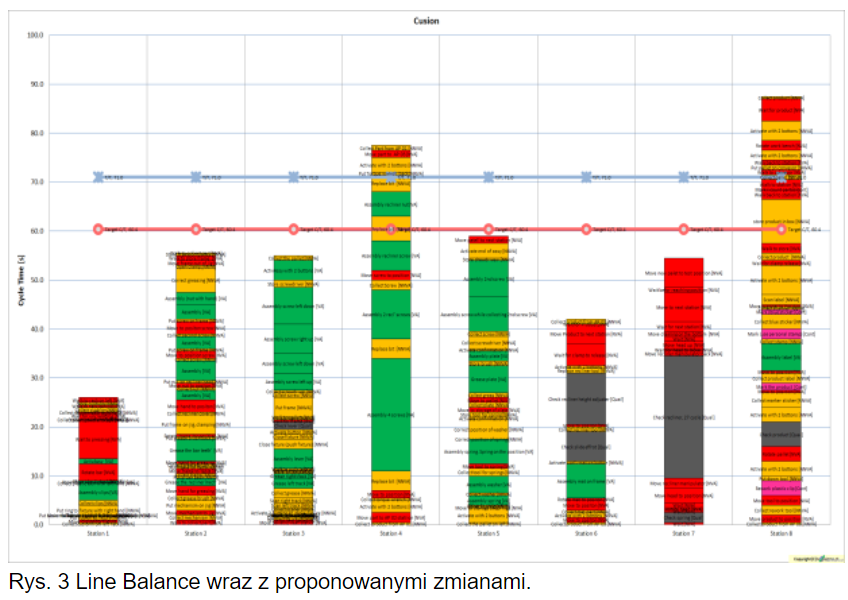
Ktoś może zapytać: „Po co tyle szczegółów na tym wykresie?”. Faktycznie analiza filmu, który trwa 120 s może zająć 30-60 min. Natomiast mając wszystkie detale mogę odpowiedzieć na następujące pytania:
– Jaka jest kategoria czynności: VA, NVA, NNVA?
– Czy mogę zrobić coś w krótszym czasie i dlaczego (pamiętajcie: nie chcemy szybszych ruchów i ludzi, którzy pracują z prędkościami światła, ale chcemy krótsze ruchy, np. sięgamy ręką 30 cm zamiast robić 2 kroki)?
– Czy mogę przenieść operację na inne stanowisko?
– Czy mogę zrezygnować z operacji?
– Czy mogę zmienić kolejność czynności (to również może przyspieszyć operacje)?
– Czy mogę zrobić coś łatwiej?
– Czy mogę użyć jakieś narzędzie ułatwiające montaż?
– Czy pracownik wie, jak wykonać czynność (porównując np. 2 filmy można zobaczyć osobę, która robi coś efektywnie i porównać z tą, która tego nie potrafi)?
– Czy mogę inaczej ułożyć materiał (bliżej, na odpowiedniej wysokości)?
Jak zakończyła się historia Line Balance w dalekim kraju? Przedstawiłem propozycję nowego Layoutu z 9-oma Stacjami oraz stanowiskiem pakowacza oraz nowy Line Balance, który jest przedstawiony na Rys. 4. Doskonale widać, że mamy rezerwę jeżeli chodzi o C/T. Pojechałem do firmy (nie daleko zakładu mojej firmy), która projektowała stanowisko testowe. Byli zaskoczeni analizą i przyznali mi rację, że mogą skrócić C/T na stanowisku zmniejszając wymiary i przeprogramowując sterownik PLC.
Po 2 tygodniach moja misja zakończyła się a zmiany wymagały inwestycji, zatem nie zobaczyłem wyników swojej pracy. Po 3 miesiącach dostałem email, że zmieniono Layout wg moich wytycznych i że osiągnięto zamierzony cel 60 szt./godz. Czegóż można chcieć więcej od życia? No chyba tylko więcej takich problemów w egzotycznych krajach :-)).
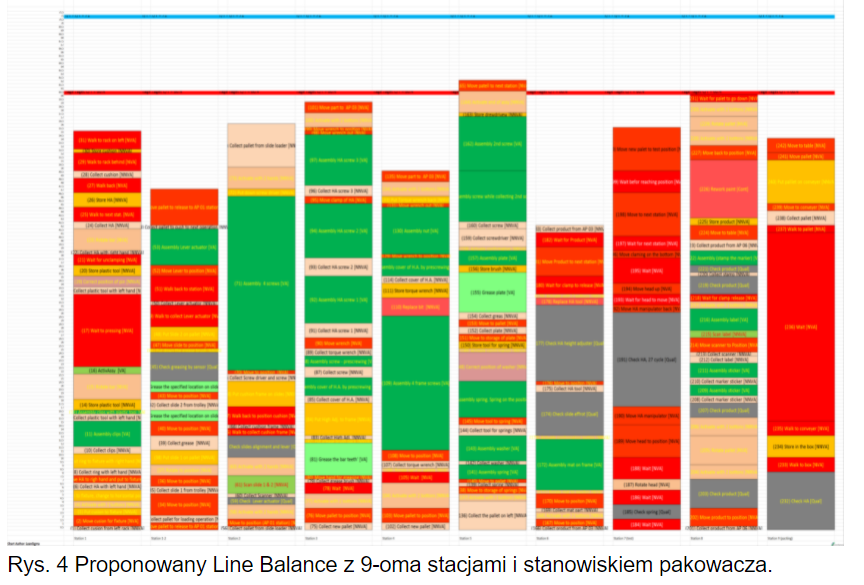
Ta sytuacje pokazała mi, że ludzie, którzy wiedzą bardzo dużo o produkcie i produkcji, często zmierzają do wniosków i do rozwiązania bez potrzebnej analizy. Nie można od tak sobie zrobić balansu linii. Mnie to zajęło 2 dni, ale nie był to czas stracony.
Czego nauczyła mnie historia Line Balance w dalekim kraju?
– Ludzie mówią Line Balance, ale myślą zupełnie różne rzeczy.
– Ku naszemu zaskoczeniu możemy nie zdawać sobie sprawy ze skali marnotrawstwa w procesie.
– Często pomijają ważne szczegóły.
– Ludzie przechodzą do rozwiązań bez należytej analizy.
Tak się dobrze składa, że przygotowałem dla Was Line Balace Chart do pobrania.
PS. Autorem artykułu jest Adam Cetera, który jest trenerem The Lean Six Sigma Academy Poland oraz certyfikowanym Six Sigma Master Black Belt’em z ponad 20-letnim doświadczeniem w optymalizacji procesów. Więcej informacji o naszym trenerze możecie znaleźć na jego stronie: www.leansigma.pl. Bezpośredni link do artykułu: https://leansigma.pl/?LANG=POL&Knowledge=LineBalanceSA